Shear-Free or Elongational Flow And Viscosity
The elongational flow properties of polymers are of great importance in polymer resin processing such as film blowing and fiber spinning and are essential in the design of processing equipment, process optimization, and troubleshooting.
In analogy to the shear rate, the elongational flow rate is defined by:
dε / dt = dv / L = L-1 dL / dt
and the elongational viscosity (also known as extension, tension, traction or stretching viscosity) is defined by
λ = σ / (dε / dt)
where L is the length of the tensile bar and ε is the true strain (also called Hencky strain). If the material does not flow, the equation above simplifies to Hooke's law:
E = σ / ε
where E is the Young's modulus. It is the slope of the stress-strain curve.
Velocity Field of Uniaxial Elongational Flow
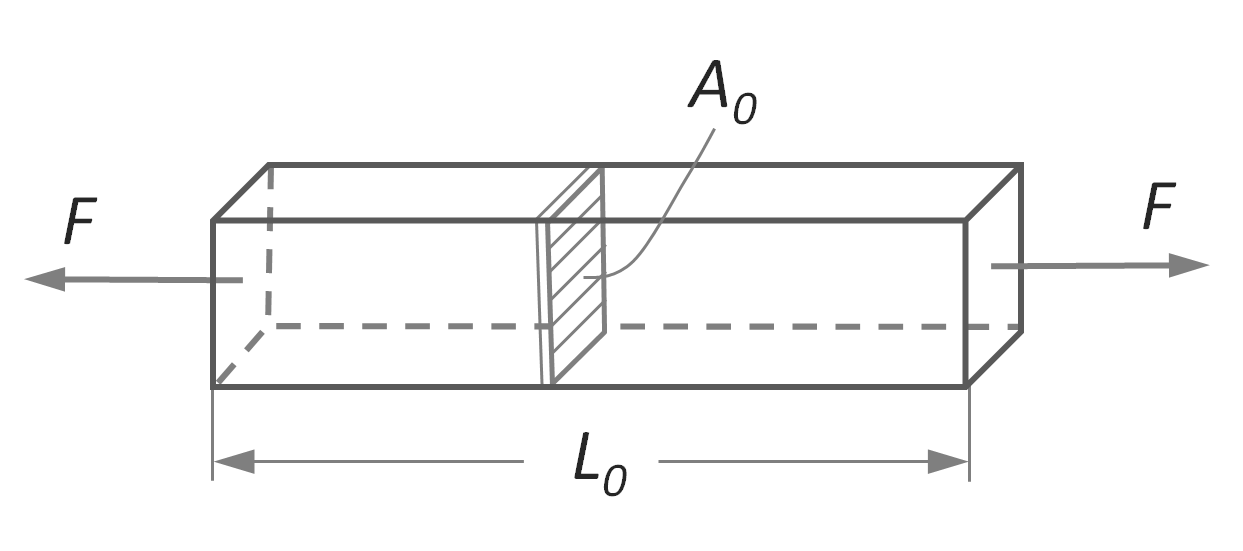
Three types of pure elongational flow behavior may be observed:
The tension viscosity is independent of the elongational flow rate and is equal to three times the zero shear viscosity.
λ = 3 μ
These materials are called Troutonian materials and the viscosity is often referred to as the Troutonian viscosity.The elongational viscosity increases with tensile stress. This behavior is known as tension stiffening. It is the analog to dilatancy in shear flow.
-
The elongational viscosity decreases with tensile stress. This behavior is known as tension thinning. It is the analog to pseudoplasticity or shear thinning.
Tension stiffening has been observed for low density polyethylene (LDPE), whereas linear olefins such as high density polyethylene (HDPE) and polypropylene, exhibit tension thinning when exposed to high tensile stress (elongational flow rates). Most other polymers appear to be Troutonian materials, that is, the tension viscosity is more or less independent of flow rate. This includes polymethyl methacrylate (PMMA), polystyrene (PS), polyethylene terpehthalate (PETE), polycarbonate (PC) and polysulfone (PES).
There are three simple types of shear-free elongational flow experiments that can be conducted in the laboratory:
Uniaxial elongational flow: The sample is stretched in one direction. vx = dε/dt; vy,z = -½ dε/dt
Biaxial elongational flow: The sample is stretched in two directions. vx = dε/dt; vy = dε/dt; vz = -2 dε/dt
Planar elongational flow: The sample is stretched in one direction but contracts in only one direction. vx = dε/dt; vy = -dε/dt; vz = 0
In all three experiments, it is assumed that the polymer is incompressible, so that vx + vy + vz = 0. These ideal flow conditions are an oversimplification of the true flow that occurs during processing of a resin. A liquid plastic may be subjected to both shear and elongational strain and the flow might be nonuniform. Furthermore, elongational flow during processing is usually non-isothermal and often results in a phase change to a semi-crystalline or solid (oriented) amorphous state.
Below, we will discuss in more detail the uniaxial elongational flow. In this case, strong stretching occurs in the x-direction and contraction occurrs equally in the y- and z-directions. The velocity field of this situation is schematically shown below.
Velocity Field of Uniaxial Elongational Flow
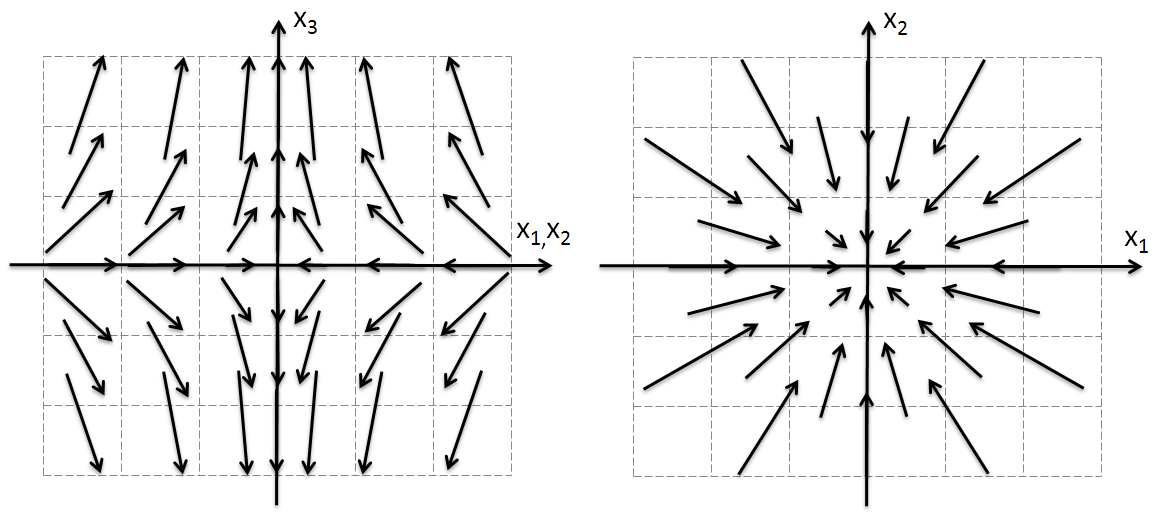
In a constant strain rate experiment, a test specimen (molten polymer rod or fiber) is stretched at a constant flow rate. This requires that the velocity v is increased in line with the specimen end separation. As will be shown below, to achieve this condition, the length of the specimen must exponentially increase in time, L(t) = L0 et·dε/dt, wheras in real processing operations the strain rates are variable.
The elongational strain may be written in terms of the true strain or logarithmic strain:
dε / dt = d{ln [L(t) / L0]} / dt
where L0 is the inital length of the specimen and L(t) is the length at time t. Since at t = 0, L / L0 = 1 and the strain rate is constant, the equation above simplifies to
dε / dt = ln[L(t) / L0] / t
To calculate the stress at time t, both the tensile force F(t) and the corss-sectional area A(t) at time t have to be measured:
σ(t) = F(t) / A(t)
However, it is much easier to measure the length of the sample. For incompressible materials,
L(t) / L0 = A0 / A(t),
it follows
σt = F(t) / A(t) = F(t) / A0 · [L(t) / L0 ] = F(t) et · dε0/dt / A0
whereas for the tension viscosity (elongational) λ it follows
λ = σ(t) / (dε / dt) = t σ(t) / ln[L(t) / L0] = (t F(t) / A0) · et · dε / dt / ln[L(t) / L0]
References
- F.T. Trouton, Proceeding of the Royal Society, Vol. 77, Issue 519, page 426 (1906)